cherry wood dining room set
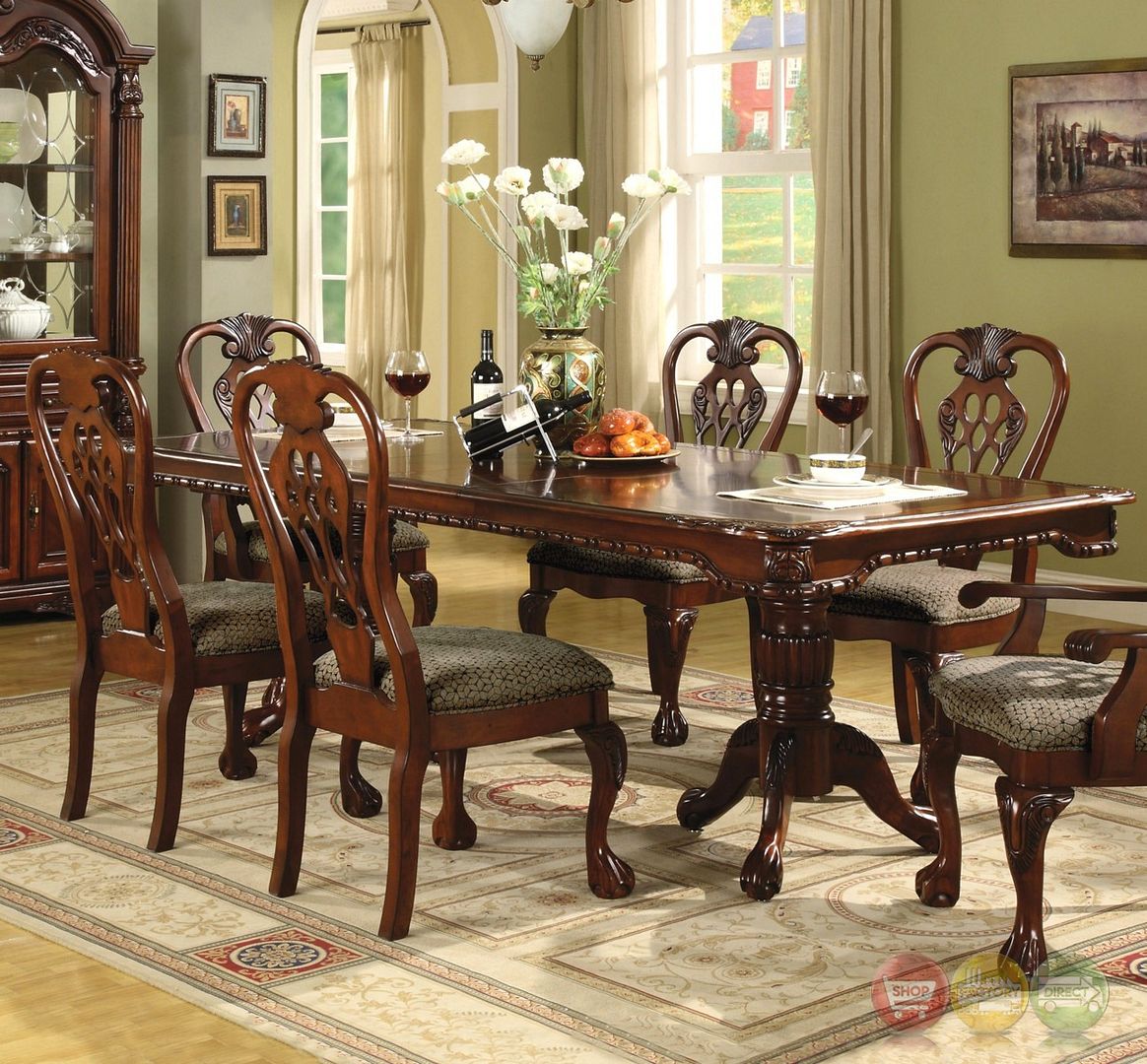
i'm brad rodriguez for fix this build that and today i'm going to show you how to make an epoxy waterfall river table. now this is my first time working with epoxy and my first time welding. so i'm going to show you some tips and tricks along the way stay tuned. i'll show you just how i did it. i dad this old cherry slab for awhile and i never knew what to do with it because it was so curved and gnarly. but one day it hit me this would be the perfect piece to rip in half and give me a live edge river table. to find the best cut line i used a string and i centered it on the end of each slab i played around with it until i found the line that i wanted and i marked both ends for the cut.
now the slab was about as warped as it was curved so i shimmed it from underneath for a stay base. then i clamped a straight edge to the slab and i used my cordless circular saw from ridgid the sponsor of today's video to cut the slab in multiple passes. and the slab was just a little thicker than the depth of my blade so i had to finish off the cut the old fashioned way, by hand. with the slab cut into two halves, i took them through a few milling operations to get the board's ready for the next step. i surfaced the slabs flat on one side with my joining, then i used that reference surface to flatten the other side with my planer.
having two flat and parallel faces i went back one more time to the jointer to get a square flat edge on each slab. with the slabs cleaned up i could tell that they were too long and a little bit too thick for what i wanted to do. so i found the best part of each slab and then i cut them to length for the size that i needed using my table saw and once again a handsaw. now instead of just planing off and wasting the extra thickness of the slabs i resawed each of them down to an inch and a quarter. now i'll be able to use the thinner pieces from this cut off in another project later. i ran the boards through the planer one final time to remove the bandsaw marks. and then i cut the slabs to final length for the form that i'll be making.
to prep for the resin pour i needed to clean up the live edges by sanding off any loose material and got a good surface for the epoxy to stick to. like i said the slabs were pretty gnarly and had some good size checks and cracks in them some going all the way through the edge. so i taped up the bottom of the cracks and then i mixed up some five-minute epoxy to fill the voids. this is gonna help me stabilize the edge and keep the epoxy from leaking out during the main pour. now while the epoxy was setting up i moved on to making the form for the pour. i had some 3/4 inch mdf on hand and i cut a base in four sides out of it
to keep the epoxy resin from sticking to the form i covered the pieces in a sealing tape. i'll have a link down below in the description to this tape and all the other items that i use during this build. i put the form together with screws and then sealed the inside corners of the form with more of the tape. now if i did it again, i'd probably use silicone to seal the inside corners because the taping took quite a while especially on those inside 3-way corners. i loaded the slabs into the form and i could really see the shape starting to come together this thing is gonna look awesome. now to keep the slabs from floating around on the epoxy i clamp the wood down and i screwed it to the form from underneath
you could also just clamp them down if you don't want the holes on the underside. i used a hot glue gun to seal up some small gaps on the ends of the slabs too to try to keep that epoxy out. now the form needs to be level for the epoxy pour so i shimmed up one end of my bench to make sure that everything was even in level. next i figured out how much epoxy resin to use. i measured the gap between the slab in 4 to 8 inch segments at a time then i multiply that average gap by the length of the segment that i was measuring i added up all those numbers and then i multiplied it by the height of the slab so i could get a total volume of the gap.
now to convert to leaders i called in an expert. alexa how many liters is 155 cubic inches i used an epoxy with a two-to-one resin to hardener mix. i wanted a two-color pour so i measure out one and a half liters of the two makes in one container in one later in the other i added some metallic pigment to the epoxy and i stirred each mix for several minutes the deep blue and the green turned out amazing and that silver pearlessence gave it some extra depth. now for the big moment of the pour i decided to pour it from both ends one color in each hands a shout-out to my buddies dylan and jason of black forest wood co
who showed me how to do a pour like this on one of my instagram lives. and while the epoxy was curing i actually went to cleveland for a spring make event with lincoln electric. they brought a group of youtubers and local makers together to teach us how to weld better. i was the newbie of the bunch. and i just learned the basics of mig and tig welding i went to a local metal shop and i picked up some one-inch square tube for the base and i used the lincoln 210 mp to weld up the base. it was really easy to learn with that digital readout. i'm really excited to do more welding projects in the future. thank you - lincoln electric for having me out and
to doug from retro weld and john malecki for helping me film this and build the base. back home, i grinded the welds down on the base with my grinder and a flat disc. it was nice to have a cordless grinder here so i could grind it in the side yard and keep that metal dust out of the shop. i drilled mounting holes in the base for the top. and then i primed it and sprayed on some matte black paint in a matte clear coat it's not perfect but it was a great learning experience in a great first welding project with the epoxy 72 hour cure complete it had setup rock-hard. i unscrewed and removed the sides from the form, and then i removed the screws from the bottom of the slab.
to separate the slab from the form i used a putty knife and a small pry bar to work around the piece until it released you could see on the backside that quite a lot of the epoxy ended up leaking under the slabs and this brought the top surface of the epoxy down below the wood a bit. i purposely made the top just under 13" wide so i could use my rigid 13 " planer to level the wood in the epoxy. and remove any excess from the bottom very easily you could also use a belt sander for this step and on larger pieces that can't fit in the planer after the planing a few voids showed up on the surface so i filled them in with five-minute epoxy, and i used some that blue pigment to make sure that it blended in with the pour. instead of sanding it all off after the epoxy cured
i just ran it through the planer again at the same settings and it worked like a charm. besides in one in needed to be cleaned up next so i squared up one edge on the jointer and i trim the other side on my table saw. i also squared up one of the ends on my crosscut sled and then started final prep on the slab before making the waterfall joint. i went ahead and sand of the slab now since it seemed like it'd be easier to work with in one piece. i sanded the wood up to 180 grit and i took the epoxy all the way up to 400 grit. i probably do the sanding after the glue up next time because it did get a little bit scratched up during the next few processes.
i used my table saw on a crosscut sled to cut the waterfall edge on the table i tilted the blade to 45 degrees. i made the initial bevel cut on the larger vertical piece then i flipped the smaller top piece over and i back beveled it with a matching miter. i moved the blade back to 90 degrees and then i cut the larger piece to the exact size for the base. there's several different ways to do the glue up for a long miter joint like this and i opted for what i think is the easiest one. i lined up the two pieces with the minors facing down, and i put a piece of packing tape across the seam. then i flipped over the pieces and put two more pieces of tape just past the miters to stop the squeezed out from getting on the wood.
after that i folded up the miter and i used the top to position and clamp down a pair of right angle squares to the slab this gave me a great reference base. i used five-minute epoxy again for this connection. i applied it liberally to one side of the joint then i folded up the miter and clamped the top to the right angle squares that were already clamped down to the bench. now if the miner wasn't fully supported by the metal base i would have used splines or a floating tenon to strengthen the joint
but i didn't think that that was needed here because of that support from the metal. i let the epoxy set up overnight and i took it out of the clamps to the next day. the miter turned out really well and all i needed to do is some final sanding before finish. i applied a two-part oil-based finish to the slab and the cherry and the epoxy really came to life. the knots, spalting and grain variation in the cherry really popped against the depth and the color of that blue epoxy resin. i buffed the oil off the surface and i was ready for the base. i meant of the base upside down, and i shim the wood as necessary to fit my less than perfect welding job.
i left the top of the base open in the back you can see here why i did that so there'd be no metal crossing under the epoxy and obscuring the light passing through it. and this project really challenged me to try new things it was fun to work with new materials like metal and epoxy and i'm looking forward to incorporating them into future projects. i want to give big thank you to ridgid power tools for sponsoring my channel and today's video. there's a link down below in the description and you can read about all the new ridgid power toolss that they have coming out with their 10 inch sliding miter saw their octane lineup with 6 amp hour batteries and all the promotions they have going on so go check that out .
now that i've done a little bit of welding and some epoxy work i want to do some more. tell me down below in the comments what do you think i should make next i'd love to hear your thoughts. if you're not subscribed to the channel already i'd love to have you as part of the team and until next time guys get out there and build something awesome!